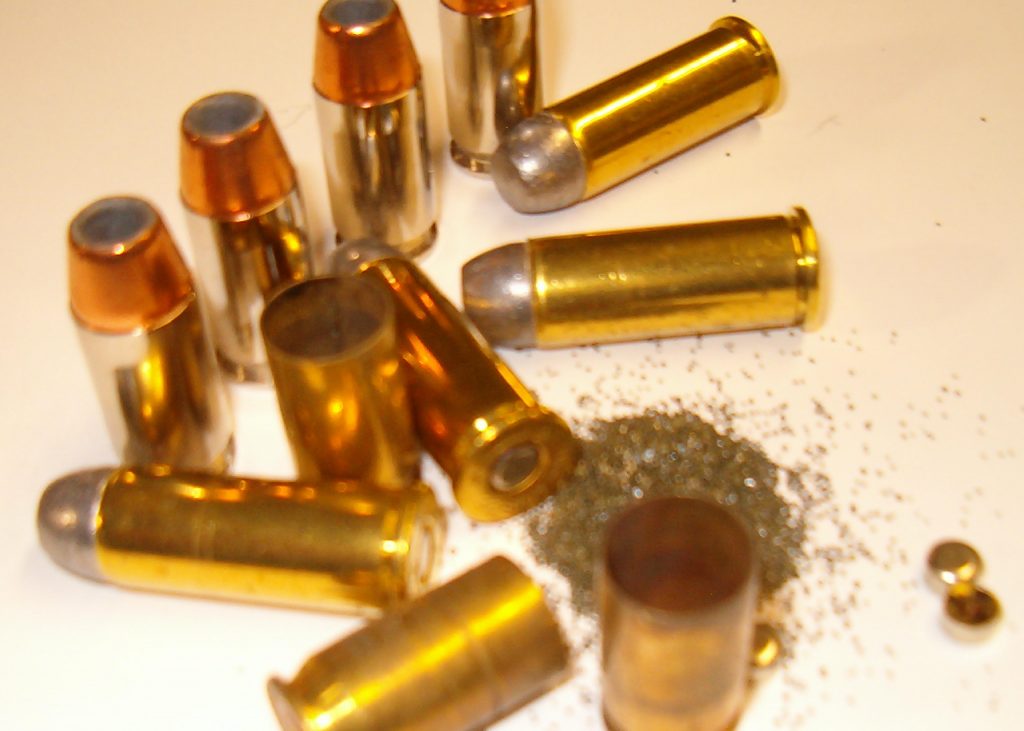
A Technology Not Yet Cultivated
We have seen a variety of efforts to decentralize the fabrication of firearms. More than a few websites offer partially completed (“80%”) receivers with instructions on how to complete them. Others broadcast canned programs designed to produce plastic guns through additive manufacturing and stereolithography techniques. Yet others provide demonstrations of rifling machines.
Those who take the time to research the matter will find worthwhile articles, books and videos providing instruction in gun design and the manufacture of firearms. The really useful offerings are small in number, but they are available and have an audience. The same cannot be said of instructional materials on the subject of ammunition. While the sale of reloading components is a substantial business, where can one find educational materials addressing the small scale manufacturing of cases, primers, projectiles and powders?
Persistent study of ammunition manufacturing will reveal that there are no inherent obstacles to the artisanal manufacture of the named components. There is no identifiable reason why cases, propellants, primers and projectiles should only be produced by large manufacturing concerns. Indeed, movements to decentralize ammunition making have arisen at several points in the history of the United States. The first example that comes to mind is the attempt to popularize local “laboratories” during our Civil War, when a want of ammunition was keenly felt.
The lack of widespread knowledge in this area is not merely curious; it is also unfortunate and inexplicable. Firearms are of little use without a reliable supply of ammunition. Supplies of reloading components are unpredictable, being the output of obscure processes, coming to users from remote locations, and always at the mercy of regulatory whims and interruptions in transportation systems.
I submit this situation can be remedied by diligent study and experiment. Some areas of inquiry come to mind:
- Can the process of brass extrusion be adapted to a small scale operation?
- Is it possible to make satisfactory cases from plastics, particularly for low velocity/low pressure handgun ammunition?
- Can simple dies be manufactured to allow the manufacturing off primer cups and primer anvils in small quantities, perhaps dies designed for use in a lightweight hydraulic press?
- How difficult would it be to manufacture a swaging press for bullets, with quick change swage blocks for a variety of calibers?
- What formulas can be located for primers and propellants, using materials generally available, or that can be synthesized from materials readily obtained?
A look back at the history of ammunition development might be helpful in this regard. Until about sixty years ago, primers were loaded with rather simple chlorate based mixtures from which highly unstable materials such as fulminates and TNT were conspicuously absent. A smokeless power based on ammonium nitrate (“ammonpulver”) has been used at various time as both a small arms and artillery propellant. Is it possible to elaborate upon these technologies to pave the way for accurate and reliable locally manufactured ammunition, produced in small quantities?
This post is as much an inquiry as it is a statement, and I invite readers to respond with any comments they deem helpful. If you have any information which you think useful, please let us know!